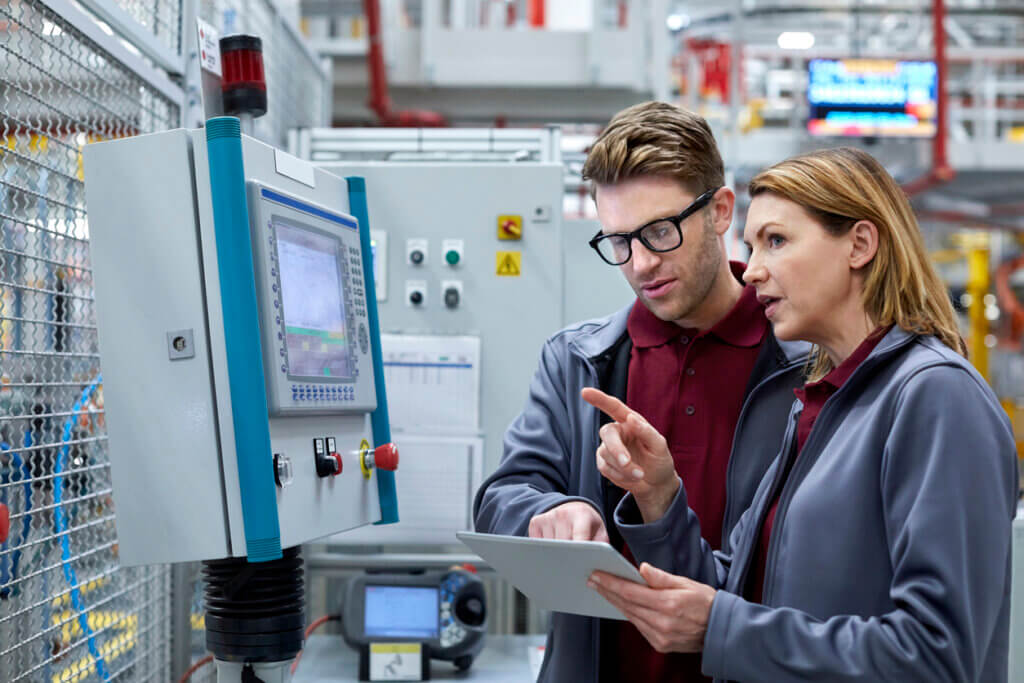
In Ireland and throughout the world, the manufacturing landscape is changing beyond recognition. The adoption of digital technology is now a bare essential in today’s fast-paced marketplace, and businesses must stay ahead of the trend to maintain employability and profitability. In the latest blog from the AMTCE, we explore 6 ways Irish businesses can upskill their workforce to meet this new demand.
Before we get started, let’s take a look at some of the facts behind advanced manufacturing and the labour landscape which has driven its growth.
Over the past number of decades, maintaining the competitive advantage in manufacturing has largely depended on finding plentiful sources of low-cost labour. However, with wages rising rapidly and economies growing in emerging markets, manufacturers are under growing pressure to improve their productivity via the technology they use.
Technological development is now the key catalyst behind advanced manufacturing, which many in the industry now refer to as ‘Industry 4.0’. Incredibly broad and ever-changing, advanced manufacturing is driving the digitisation of industry and helping businesses increase productivity in a way that is more flexible and environmentally friendly.
So – how can Irish businesses get onboard with these revolutionary changes? Let’s take a look…
- Convince Your Workforce
Manufacturing spaces throughout the world are adopting digital technologies at an unprecedented rate, with a study conducted by the US Manufacturing Institute finding that US businesses planned to spend $26 billion on upskilling in 2020. However, whilst many manufacturing organisations have the budget to upgrade their technology, upgrading their workforce represents a separate and distinct challenge.
Here at the AMTCE, we believe that convincing staff and ‘bringing them along’ in the process is critical. This means persuading staff to discard tried-and-tested processes to embrace something totally new – and not all working personalities react positively to the prospect of change. Businesses can make strides in this area by showing their workforce the benefits of new processes and the increased capacity it can create.
When articulating the benefits of advanced manufacturing processes, it’s important to support your employee’s sense of security in their role. Make it clear to your staff that whilst their role may become redundant, their job won’t. Indeed, whilst technology may take a current job, it will create a new one. Getting this message across is essential.
- Prioritise Human Skills
A quick ‘Google’ on advanced manufacturing often highlights the idea that “robots will steal our jobs”. And, whilst technology is increasingly making certain jobs redundant, it is simultaneously creating a demand for skills that only humans can provide.
Regardless of your technological capacity, it is important to remember that human skills are the most valuable. By using automation to take care of repetitive, manual tasks, a space is made in digital for soft skills that can be executed by humans only.
Creativity, critical thinking and emotional intelligence are equally essential in the future of advanced manufacturing. For every effort made in upgrading your technology, be sure to invest in these traditional yet critical areas at the same time.
- Embrace Digital Communication
The success of your upskilling strategy will depend on more than cutting-edge technologies and infrastructural investment. Whilst investment in technologies like automation, AI and robotics can ultimately transform productivity, it is imperative that companies use digital solutions to handle certain processes more effectively.
So – what kind of digital solutions are we referring to? To start, collaborative platforms and workplace instant messaging tools are making virtually all jobs more digital. Unlike any other method, these solutions provide the strong communication and interaction required to sustain higher levels of productivity.
Embracing this shift also allows businesses to reach out to skilled professionals anywhere in the world, allowing businesses in less-connected areas to build a workforce that is connected, international and 24/7 in its operation.
- Use People to Drive Technological Change
All workers have something to gain from new technologies and their impact on manufacturing processes. Aside from transforming health, safety and productivity, technological development can ultimately prepare your workforce for a future where human labour is more sophisticated, growth-orientated and individually rewarding. In many cases, the introduction of new technologies and processes can be catalysed by the arrival of new talent.
The value a fresh set of eyes can bring to manufacturing processes shouldn’t be underestimated. New employees can work with your existing talent to identify areas for digitisation and process improvement, asking questions that many may have forgotten to ask.
- Change in a Way That’s Scalable
This leads to one of the most important points to remember when upskilling your workforce: don’t confuse transformation for revolution. Affecting change must be done in a way that is scalable and reasonably paced, taking those small but necessary steps to ensure you’re investing in people throughout the transformation process. Indeed, discarding old technologies and processes and immediately replacing them with something new will likely frustrate your efforts.
Getting this right means setting clear and achievable objectives. Start by mapping your current processes, identifying modest ways of improving productivity to begin with. Involving your staff in this identification process allows them to see the benefits of changing work patterns whilst actively including them in the management of the timelines involved in getting there.
6. Take Advantage of Apprenticeship Programmes
The future of manufacturing will be underpinned by advanced skills and advanced technologies. When it comes to developing those essential skills, apprenticeship programmes will play a significant role. With this in mind, manufacturing organisations should regularly review how they can expand their talent pool, with a special focus on partnership with universities, colleges and training centres of excellence.
All stakeholders have something to gain from a strong apprenticeship partnership. Whilst it will allow the learner to attain valuable qualifications at an often-reduced cost, it will also provide your company with a skilled employee at the end. To find out how your business can invest in an apprenticeship programme via the AMTCE in 2022, contact us.
Advanced Manufacturing: The Future is Now
A skilled workforce which evolves in response to technology advancement and opportunity is critical to the sustainable success of companies as they navigate through the digital transformation of their businesses. Here at the AMTCE, we provide a range of courses and apprenticeship programmes to help Irish businesses adapt for the future. To learn more, browse our full range of courses or contact us to discuss personalised learning opportunities.